20 Oct Tailgate Meeting – A Job Hazard Analysis Technique
In a speech given at the National Defense Executive Reserve Conference in 1957, President Eisenhower said, “Plans are worthless, but planning is everything. There is a very great distinction because when you are planning for an emergency you must start with this one thing: the very definition of “emergency” is that it is unexpected, therefor it is not going to happen the way you are planning.”
The truth is that life rarely goes the way we plan, but every one of us leaves the house with at least an idea of what we are doing that day and, over time, we develop planned responses to the occurrences in our lives. We should do no less in our professional lives.
Furthermore, we have a moral duty and a legal obligation to protect our employees from the dangers they face while executing the tasks they perform in the name of their employer.
Whether you call it a Job Hazard Analysis (J.H.A.), Job Safety Analysis (J.S.A.), Tailboard Meeting, Tailgate Meeting, or old school Safety Brief, the task is the same. We must identify potential sources of harm to the employee and mitigate those hazards, bringing the risks into an acceptable degree.
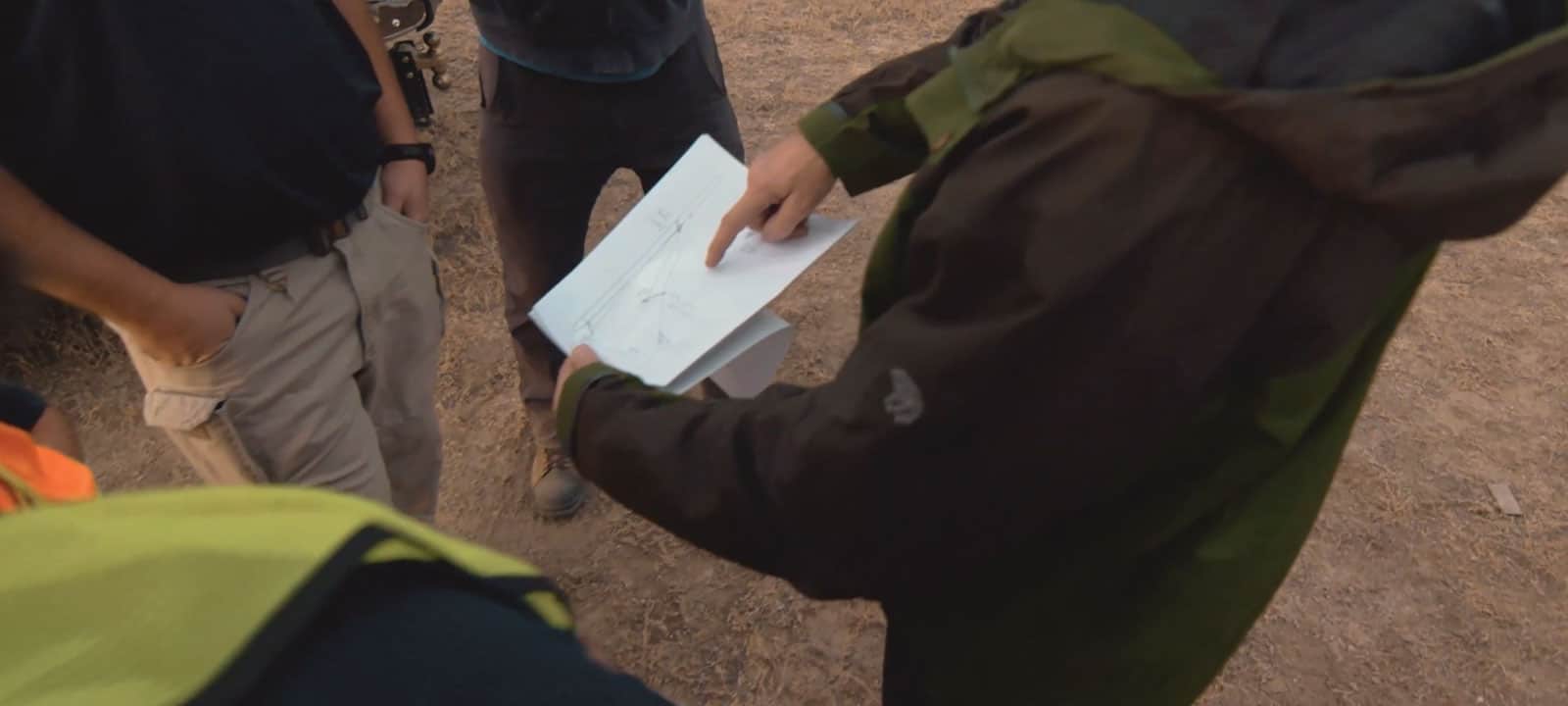
Job Hazard Analyses contain four basic parts.
DEFINE AND DETAIL THE SCOPE OF WORK
The first section of the document will detail the scope of work. In this segment, the tasks are discussed. Often times, when asked what we begin with during the J.H.A., the response is “hazards,” however we cannot identify hazards until we know what we are doing for the day. Once the associated tasks and tools have been identified, the associated hazards can then be discussed.
DEFINE HAZARDS
Hazard identification can be difficult as it tends to depend on our level of familiarity with the work being done and the environment in which it is being conducted.
In order to assist with this task, a tailgate meeting checklist can be generated and provided to the crews. This checklist will contain commonly found hazards for the expected environments and tasks. Frequently, tailgate meeting forms and safety checklists are provided by the employer.
Good training can also supplement field experience. Once safety concerns are identified, mitigation can be established.
HAZARDS MITIGATION
There are several forms of mitigation in the case of work place hazards. The preferred method is to engineer the hazards out of the environment or the machinery being used.
If that is not possible, administrative controls can be set in place. These will provide procedures in lieu of the engineered controls aimed at protecting the worker. Finally, the last line of defense can be personal protective equipment.
Once, tasks, hazards and mitigation have been decided upon, the last question that needs answering is “What do we do if it all goes wrong?”
EMERGENCY RESPONSE AND RESCUE PLAN
The emergency response or rescue plan is essential to dealing with the unexpected. While, as President Eisenhower said, we cannot expect an emergency to go the way we planned, making sure critical skills and information are in place before hand is essential.
Information such as emergency contact numbers, hospital location, and the availability of emergency services is critical to minimizing response times to life threatening incidents.
Proper placing of first aide and/or rescue equipment is also paramount to maximizing the survivability of the employees in unforeseen circumstances.
While the complete and total elimination of emergencies may be seen as an ambitious goal, proper planning and preparation for accidents can help to minimize the impact of those occurrences. Not only is hazard mitigation and training a worthwhile investment in the worker, it’s a legal obligation.
Be safe, plan well, and live long.
For more information about tailgate meetings and Job Hazard Analysis, contact us via:
Email: [email protected]
Phone: +1 (800) 485-7669
Contact us online: https://safetyoneinc.com/contact/
Safety One Training is the leader of fall protection training, snowcat/extreme-weather condition training, and safety & survival equipment. If you have any further questions regarding the training courses we provide, click here to contact us or give us a call at +1 (800) 485-7669.
No Comments